Platin-RTDs (Resistance Temperature Detector) zeichnen sich durch eine positive und nahezu lineare Widerstandskennlinie gegenüber der Temperatur aus, die durch die Norm DIN EN IEC 60751 klar definiert ist.
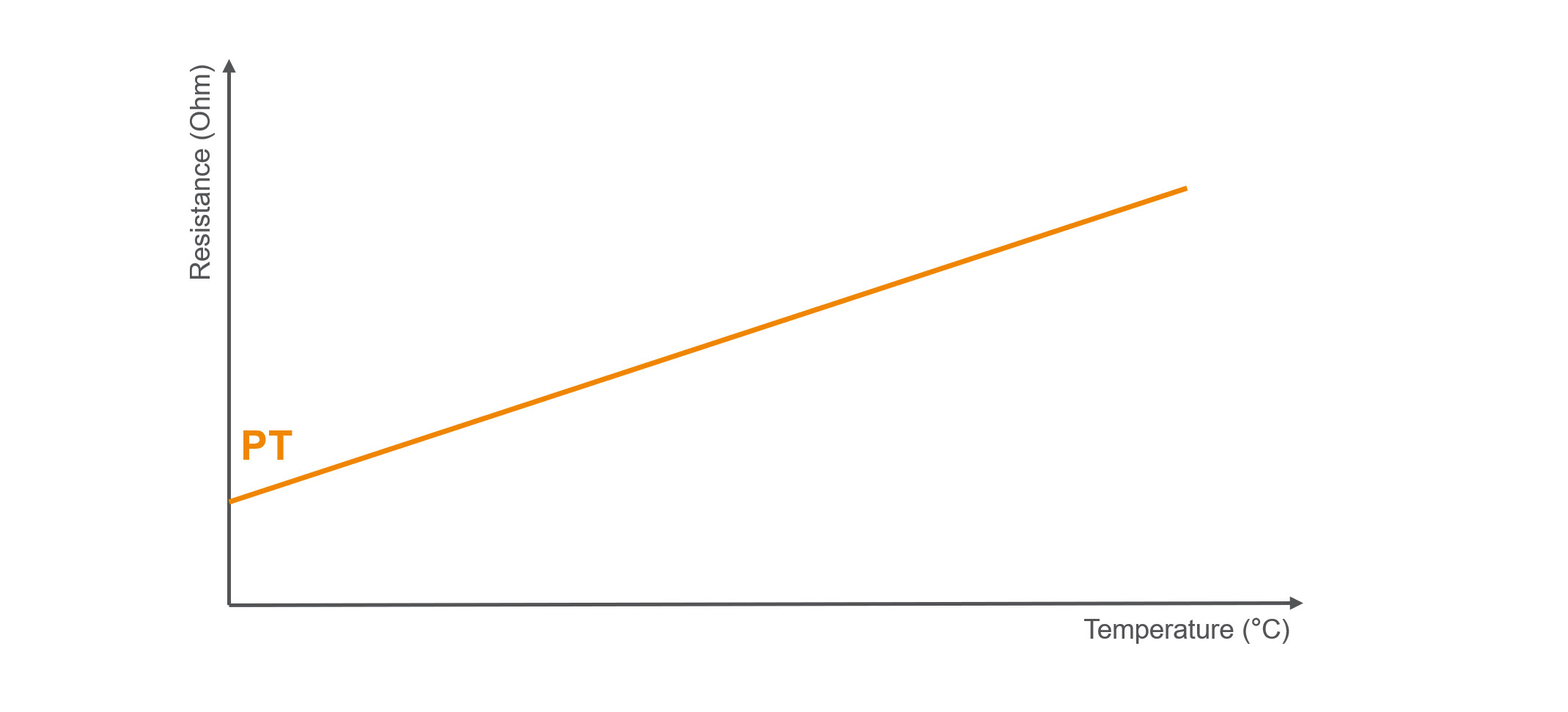
Positive linear resistance characteristic of Pt temperature sensors
Platinum-RTDs (Resistance Temperature Detector) are characterized by a positive and almost linear resistance vs. temperature characteristic, clearly defined by the DIN EN IEC 60751 standard.
A structured platinum meander is deposited on a ceramic substrate using a thin-film process. The Pt meander functions as a thermally sensitive resistor. The voltage drop across the sensor is measured with high precision and converted to a temperature value. Other versions of platinum RTD sensors are constructed using wire wound technology. Platinum-based sensors operate over a wide temperature range, from -196 °C to 1000 °C.
NTC (Negative Temperature Coefficient) thermistors are manufactured from metal oxide semiconductor ceramics, typically produced by a thick-film or compressed powder process. They feature a negative and exponential resistance change in response to temperature change. The change in resistance (voltage drop) can be converted to a temperature value. The typical operating temperature window is narrower than for Pt elements: -55 °C to +150 °C for standard epoxy-coated chip thermistors and -55 °C to +300 °C for glass-coated chip thermistors.
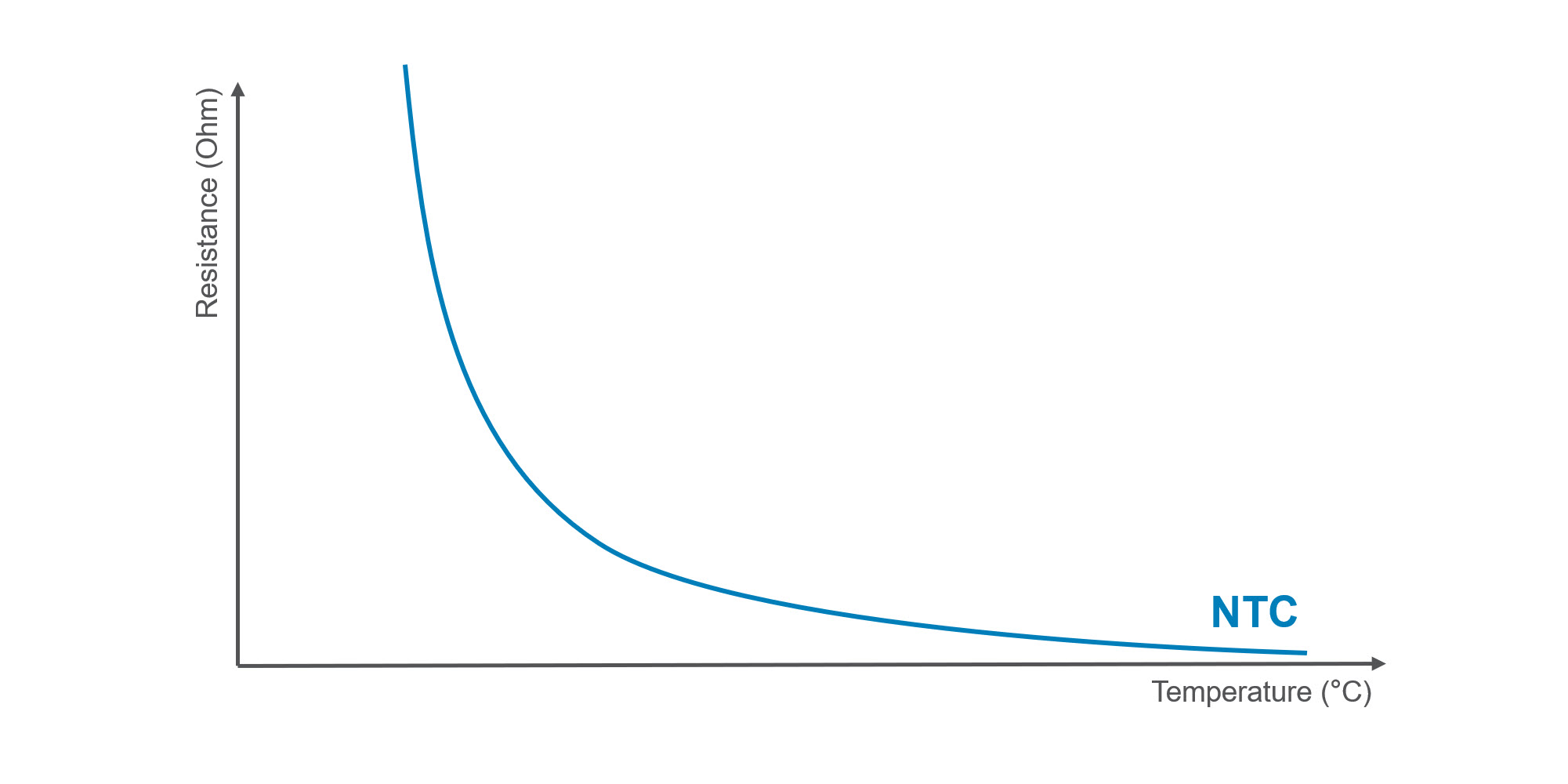
Negative and exponential resistance curve of NTCs
Pt | NTC (typical) | |
Characteristics Curve | - Positive and nearly linear TCR - TCR: 3850 ppm/K typical - Characteristics standardized to DIN EN IEC 60751 |
- Negative non-linear TCR - Typical slope: -4.4 %/°C @ 25 °C |
Typical Resistance Value | pt100, pt200, pt500, pt1000 | 2.252k @ 25 °C, 10k @ 25 °C, 20k @ 25 °C |
Configurations | - Elements with lead wires - SMD packaging, SOT223, TO92 |
Epoxy or glass encapsulation; diode package, SMD models, other variations |
Composition | Platinum thin film meander on ceramic substrate | Ceramic-metal-composition |
Operating Temperature Range | -196 °C to 1000 °C | -100 °C to 300 °C with special types up to 750 °C |
Why to use a Platinum-RTD Sensor?
The Pt-RTD has a linear signal characteristic that conforms with the universally recognized DIN EN IEC 60751 standard. This standard provides a clear definition of sensor signal output and tolerances and ensures easy sensor selection and interchangeability. In addition, it allows standardization of electronics and software. While NTCs from different manufacturers may have similar signal output, a universally recognized international standard for NTCs is not available.
Platinum sensors have a high degree of accuracy over a broad temperature range; F0.3 tolerance applies to a temperature range of -70 °C to +500 °C. NTC thermistors are available with high accuracy, but typically over much narrower temperature ranges, such as 0 °C to +70 °C. NTC manufacturers refer to a high accuracy at 25 °C, which usually contributes to a comparable small temperature range.
Temperature sensors are subjected to significant stress during use, especially at high application temperatures. Platinum, a noble metal, having the ideal properties of high-temperature capability and chemical resistance, is an ideal material for temperature sensing. Compared to NTC thermistors, platinum temperature sensors have superior drift behavior and higher long-term stability, better repeatability, and higher temperature capability.
Pt | NTC (typical) | |
Measurement Drift | - Very low drift - Typically 0.04 % after 1000 hours at 500 °C |
Nominal resistance drift: typically 0.35 % after 100 hours at 150 °C |
Accuracy | - High accuracy over a wide temperature range Defined in DIN: - Class F 0.3 / B: ± 0,12 % (± 0.3 °C) @ 0 °C - Class F 0.15 / A: ± 0.06 % (± 0.15 °C) @ 0 °C - Class F 0.1 / 1/3B: ± 0.04 % (± 0.10 °C) @ 0 °C |
- High accuracy over a relatively narrow temperature range - Typical: ± 1 % @ 25 °C |
Long-term Stability | Superior long-term stability at high temperatures | - Stability of NTC and requirement of the application should be matched - Glass-coated NTCs have a higher stability than standard epoxy-coated NTCs |
Repeatability | High accuracy and low drift support high repeatability over a wide temperature range | Good accuracy in limited temperature ranges, accuracy depends on lifetime and application temperature window |
Platinum – the Foundation for Precise Data
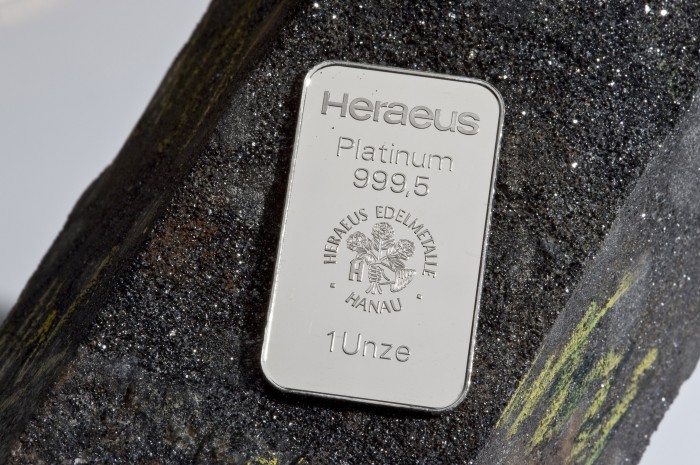
Precise temperature data is the key to controlling many processes. Only when the baseline situation is accurately known can it be usefully controlled and optimized.
The challenge generally lies in determining the situation under the conditions of actual use, which are often demanding. In some cases, the temperature must be measured with particular accuracy; in some cases, the temperatures are especially high or low. Sometimes both are true in the same application. Sensors may be required to withstand aggressive substances or constant stress during continuous operation.
If the environmental conditions change rapidly and markedly, the sensors must function reliably under a wide range of conditions while still delivering data of uniformly high quality. Platinum temperature sensors are generally the best choice, because they provide especially precise measurements over a broad temperature range, even under difficult conditions, and they are reliable and long-lasting.
Implications on the Entire Measurement Chain
The performance and cost of a temperature measurement element should always be considered in the context of the overall system and measurement requirements. A temperature sensor achieves the highest performance when appropriately adapted to the application environment and the signal processing electronics.
In applications with lower and narrower temperature ranges, and low accuracy requirements, the user can benefit from the high resolution of the NTC resistor. This benefit is maximized for small temperature ranges at lower temperatures, but significantly reduced at higher temperature due to the non-linear flattening of the NTC characteristic curve.
If the user has additional temperature measurement requirements, such as expanded temperature range and accuracy, additional challenges arise if NTC thermistors are used. Due to the non-linear resistance vs. temperature characteristic, more complex interconnection and signal processing electronics may be required. The linearization of the characteristic curve influences the accuracy of the overall system due to inherent linearization error, which is more pronounced for wider temperature ranges.
Due to the lack of international standards that define the functional properties of NTCs, care must be taken when replacing an installed sensor to insure compatibility. Often it requires additional and time-consuming re-calibration.
Using a Pt-RTD can eliminate this problem. The high measurement accuracy over the entire measurement range and the linear and standardized characteristic curve allows the use and design of standardized electronics.
For many applications, a recalibration after a sensor replacement is not necessary. In the long term, this can be a considerable cost factor, especially for more complex systems and sensor networks, as it keeps maintenance costs lower and optimizes operation up-times.
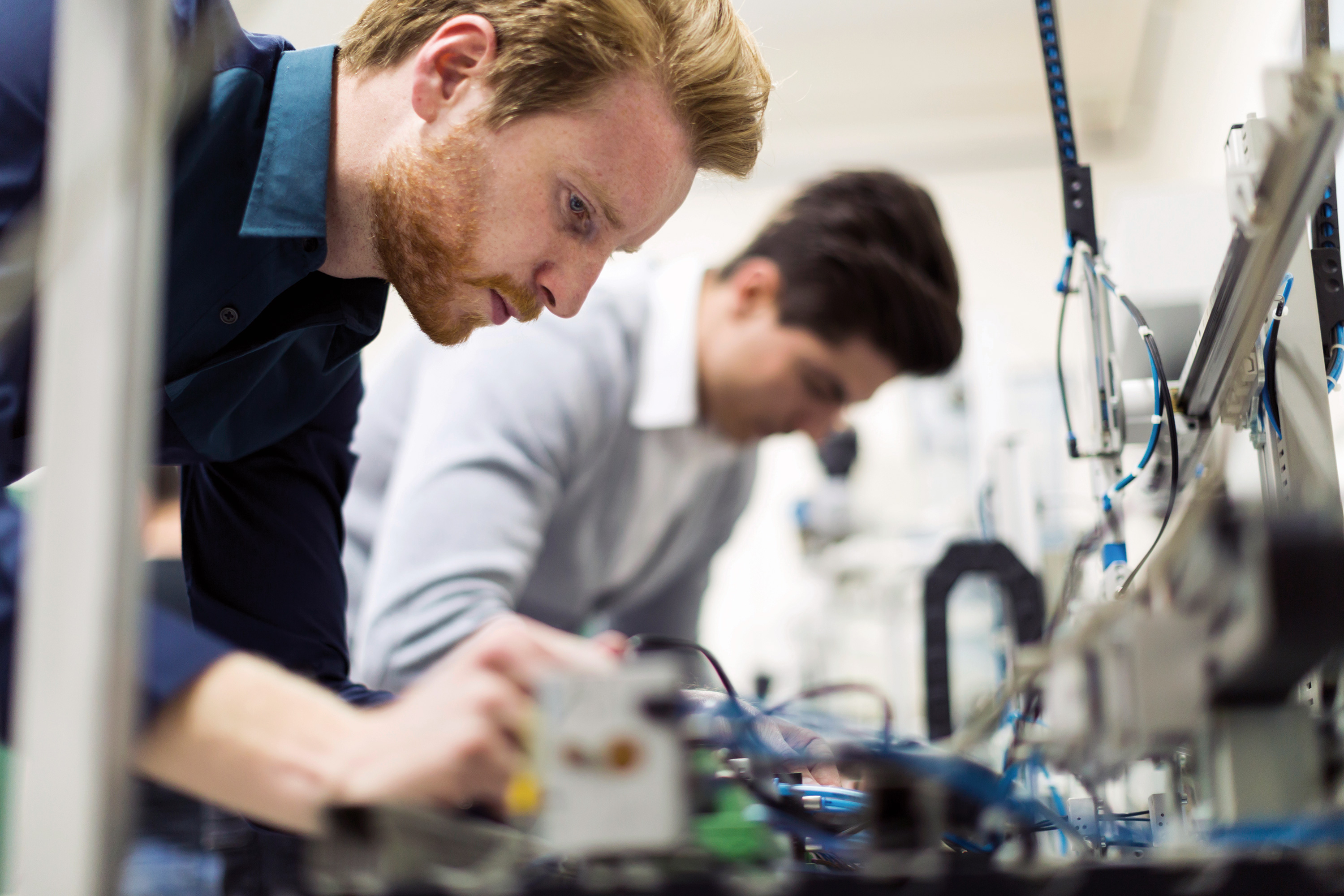