Handling
Sensors must be handled carefully to avoid damage. Plastic- or plastic-coated metal tweezers are recommended. Pliers or clamps should not be used. The element should not be subjected to any clamping forces. To avoid lead strain, the lead wires should not be bent in the vicinity of the sensor body. Avoid frequent bending or repositioning of lead wires.
Testing
Thin film elements are manufactured and tested via an automated production line, and further testing of the element is typically not required. If testing is desired, a 4-wire test fixture with low contact resistance should be used, along with a precision multimeter, 5 ½ digit resolution minimum. RTD assemblies are typically tested only for continuity.
Connection Techniques
The preferred connection technologies are welding, brazing, or soft soldering, depending upon the lead wire and temperature rating of the element. Recommended connection techniques are specified on each thin film element data sheet. Generally, welding is recommended for Ni or Pt coated Ni lead wires, and soft soldering is recommended for silver alloy, silver coated Nickel or gold-plated lead wires.
For elements with gold-alloy lead wires, such as the C416 type, only solder alloys specifically designed for use with gold should be used. Other alloys not specifically recommended for use with gold wire may cause irreversible lead wire damage.
Connection Method Details
Extension leads may be added to element leads via soldering, brazing, or welding. Typical extension lead materials are:
- Teflon-insulated silver-plated copper
- Teflon-insulated nickel-plated copper
- Fiberglass-insulated nickel-plated or nickel-clad copper
Laser welding: A laser lap or butt weld is the preferred connection technique.
Ultrasonic welding: Prior to welding, bend the leads away from the plane of the element body to eliminate internal damage.
Spot welding/resistance welding: A widely used, reliable connection technique.
Crimping: High-quality gas-tight crimping is recommended to avoid high contact resistance.
Soft soldering: Ensure that the solder alloy is compatible with lead wire material, and the melting point is higher than maximum application temperature. All flux must be removed from the element and lead wires unless a no-clean flux is used.
Brazing: During the brazing operation, the element body temperature must not exceed the maximum rated temperature. Heat sink the element leads, if necessary, during brazing, to avoid overheating. The brazing time should be less than 3 seconds.
Note: For maximum accuracy, the extension lead should be attached at the calibration point indicated on the element data sheet. Attaching the extension lead to a different distance from the element body, or cutting the element lead wire will result in reduced accuracy.
Lead Wire Length
The nominal resistance of the sensor element is measured 8 mm (with a stamdard lead length of 10 mm) from the element body. Cutting the lead wire will decrease the resistance and can shift the calibration (e.g. outside of class F 0.15 or F 0.1). This impact is more significant for a Pt100 compared to a Pt1000. Similarly, adding extension leads will increase the resistance. A 3 or 4 wire connection at the 8 mm point may be used to compensate for the additional resistance from the extension leads,
Encapsulation and Potting
The thermal expansion coefficient of the potting material should match the expansion coefficient of alumina ceramic, the sensor substrate material, to avoid measurement errors or part failure due to thermal expansion mismatch.
Rigid epoxies should be avoided, especially when the maximum operating temperature exceeds the glass transition temperature of the potting material. End-users have reported successful use of thermally conductive non-rigid silicone potting materials.
Encapsulation materials must be chemically neutral. In particular, ceramic potting materials containing fluorine compounds should be avoided. If the element is potted in a housing, the housing should be free from contaminants, such as flux, organics, etc., to avoid element damage at elevated temperature.
Please refer to individual data sheets for any requirements specific to a particular element type.
Choice of Potting Materials
Silicones: For operating temperatures below 260 °C, silicone materials are often used. Silicones introduce little strain during cure and allow for relatively free thermal expansion and contraction. The disadvantage of silicone is that it offers lower mechanical strength than some other materials. If greater strain relief is required, after encapsulating in silicone, the housing may be backfilled with epoxy or ceramic potting, or crimped, depending upon the required temperature rating. Note that some types of silicones and epoxies can mutually inhibit curing.
Ceramic Potting: For temperatures above 260 °C, ceramic potting materials may be used. The thermal expansion of the material should roughly match the expansion of alumina, the element substrate material. To avoid poisoning the element, potting materials containing fluorine should be avoided.
Ceramic Powders: For operating temperatures exceeding the capabilities of silicones, powdered high purity magnesia or alumina may be vibrated into the housing. The ceramic powder allows for strain-free thermal expansion. The housing is typically sealed with a ceramic plug.
Storage
Platinum sensing elements should be stored in a corrosive-free environment. The elements should be stored with adequate protection against shock, bending or crushing forces, etc. In high humidity environments, it may be necessary to dry the sensor before installation. To avoid corrosion elements with Silver/Palladium wires or silver coated Nickel wires should be stored in a nitrogen atmosphere.
Please refer to individual data sheets for any special handling or storage requirements.
Minimum Fit Diameter
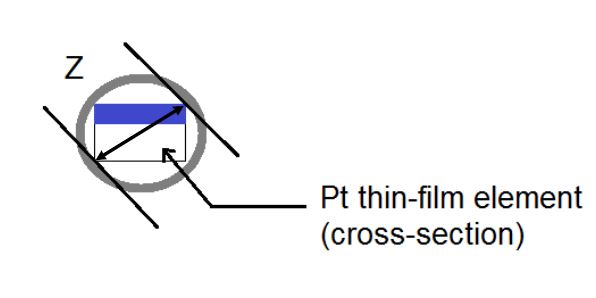
The approximate minimum fit diameter (Z) is defined as the smallest hole that the sensor element will fit into and corresponds to the diagonal of the sensor cross section.
Z = Approximate minimum fit diameter
Z2 = W2 + H2
Where:
W = maximum element width (upper tolerance limit)
H = maximum element height (upper tolerance limit)
Parts with width and height below maximum value may fit into larger diameter.